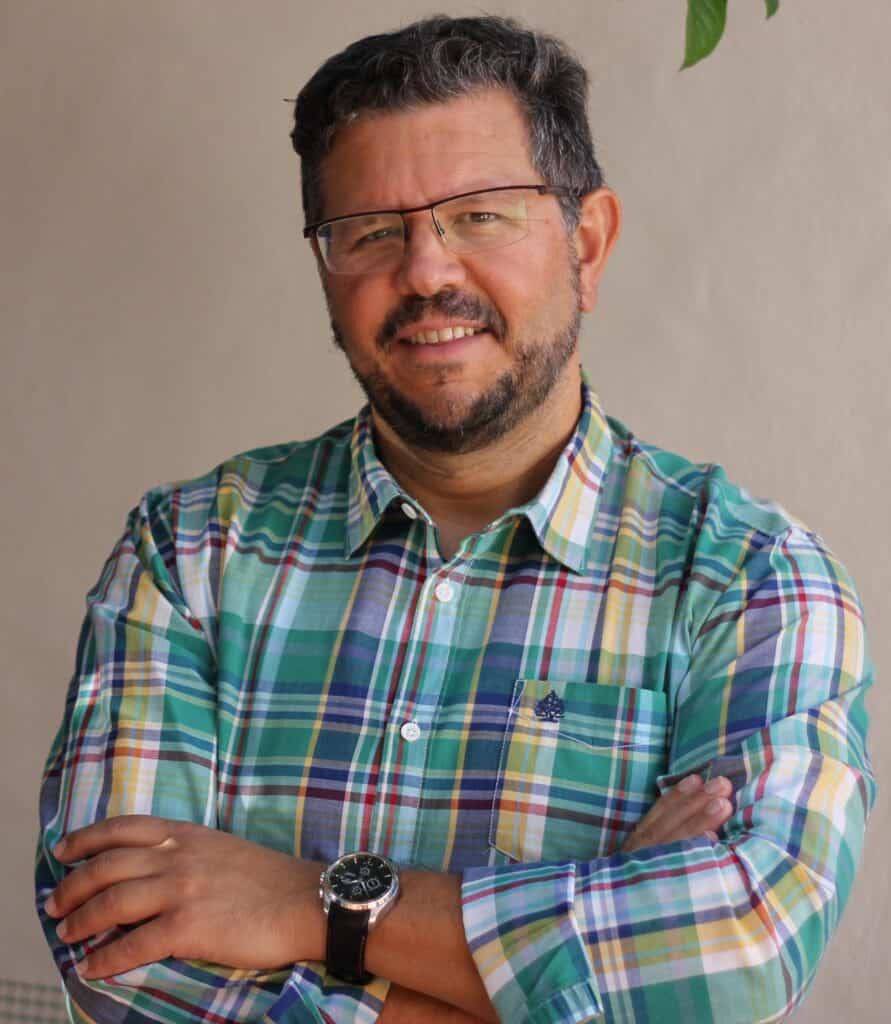
Por Miguel Santiago Calvo García, Solutions Architect en Capgemini Engineering España
La Cuarta Revolución Industrial tiene su origen en la Industria 4.0. Y ésta es el tótem actual de lo que todo el mundo habla, y que revolucionará el sector industrial en los próximos años. Y lo que es más importante, el paso obligado que deberá de dar todo el sector industrial si quiere seguir siendo competitivo y sostenible en un futuro cada día más cercano.
La industria 4.0 nos permitirá:
- Conseguir procesos productivos más eficientes y sostenibles.
- Poder tomar decisiones muy agiles tanto de producción como de negocios.
- Mejorar la gestión de los recursos y activos.
- Reducir los tiempos tanto de fabricación como de diseño de nuevos productos que se adapten a las necesidades del usuario, cada vez más cambiantes.
- Aumentar la productividad.
Todo ello con el mínimo impacto medioambiental y máxima sostenibilidad.
Para poder lograr estos objetivos será necesario el uso de herramientas como: Big data, Cloud Computing, Inteligencia Artificial, Realidad Virtual y Aumentada, Fabricación Aditiva, Gemelos Digitales, Sistemas Ciberfísicos y Robóticos. Todo esto genera la imagen de un mundo de procesos computacionales en la nube o el edge computing, y a la que a las que se accederá desde cualquier sitio.
¿Pero cuál es la base de todo esto y que a menudo pasa desapercibida? La base es la información, los datos. Sin ellos no existen ni tienen fundamento todas esas aplicaciones que tenemos en mente con sus interfaces que prometen “dirigir” cualquier fábrica desde cualquier lugar del mundo a través de cualquier dispositivo electrónico. La correcta extracción y tratamiento inicial de los datos es fundamental para alimentar el resto del ecosistema de aplicaciones que se está generando.
Debemos de tener en cuenta que los datos, en el entorno industrial, pueden provenir de innumerables fuentes: sensores de campo, autómatas industriales, robots, SCADAs, sistemas MES, sistemas de históricos, etc. Todas fuentes generan miles de valores que cambian en tiempos inferiores al segundo y que deben ser tratados en ciclos de milisegundos. Componiendo todo ello una enorme capa OT centrada en el proceso de cada industria. Por otro lado, se tiene una casi infinita capa IT donde estaban las herramientas empresariales como los ERP, que se centran en la gestión empresarial y a la que en los últimos tiempos se han añadido herramienta de analítica avanzada, inteligencia artificial y machine learnig.
Conforme han ido apareciendo estas herramientas en la capa IT se han ido solucionando las necesidades sobre cómo “alimentar” de datos a estas herramientas, utilizando desarrollos a medida, protocolos propietarios y multitud de sub-herramientas casi siempre con conexiones directas a las distintas fuentes que han generado unos entornos donde se complican las tareas de trazabilidad de los datos, disponer de dichos datos en tiempo real, poder realizar un correcto mantenimiento de dichos entornos y casi imposible crear un sistema de ciberseguridad efectivo.
Llegados a este punto, para conseguir una correcta implantación de la Industria 4.0 en nuestras instalaciones se hace necesario redefinir el proceso de integración de los mundos OT e IT poniendo el foco de este nuevo diseño en extraer el máximo de información y de la manera más segura posible en lugar de en las aplicaciones que explotan los datos obtenidos en las propias instalaciones.
Podemos hablar de tres etapas en el procesamiento de la información:
- Captura y registro digital de los datos. Los datos de los procesos físicos se extraen y se registran para su posterior uso.
- Tratamiento digital de los datos. Donde en el entorno IT serán usados por todo tipo de aplicaciones empresariales, IA, ML o analítica avanzada.
- Ejecución de decisiones a nivel de producción. Es decir, aplicar de manera directa en los distintos procesos productivos los resultados obtenidos en el tratamiento digital de la información.
La parte fundamental en la que debemos centrar la atención se concentra en lo pasos 1 y 3. Estos pasos son los iniciales que se deben acometer para una correcta integración en la industria 4.0. Para ello debemos seguir tres líneas de trabajo y algunos conceptos básicos:
La Conectividad física y Ciberseguridad. Es necesario realizar un diseño correcto de una red de comunicaciones OT que nos permita tener conexión física con todos los componentes OT de la infraestructura asegurando que se maximiza la ciberseguridad mediante la generación de zonas dentro de esa red OT para hacer más seguras cada una de las zonas por separado.
La otra línea es la Hiperconectividad, aplicar la herramienta correcta que permita garantizar la integridad de los datos, generando una única zona de consulta de los datos y proteger dichos datos en función de su uso o destino. Esta zona de consulta será donde cualquier aplicación de negocio (ERP, MES, etc…), de analítica avanzada, inteligencia artificial machine learning los consultará.
Por último, la Interoperabilidad, que asegure que los resultados de los análisis de la información inicialmente suministrada se trasladen a nivel de campo en modo de parámetros de producción (que maximicen la producción), órdenes de mantenimientos preventivos (que prevengan paradas de imprevistas de la producción) u órdenes de compra (que optimicen el manejo de stock), entre otros muchos escenarios.
Es fundamental que la empresa que decida afrontar este reto debe de asegurarse que cuenta con el conocimiento necesario o tiene un partner apropiado que tenga los conocimientos y la experiencia en los ámbitos de conectividad industrial, conocimientos de las herramientas de hiperconectividad e interoperabilidad desde servidores OPC a Plataformas IoT, y que disponga de un amplio bagaje en el sector industrial que le permitan sacar máximo rendimiento a las instalaciones existentes, oriente correctamente la nueva estrategia de conectividad y sea capaz de aprovechar al máximo las oportunidades que brinda la industria 4.0.